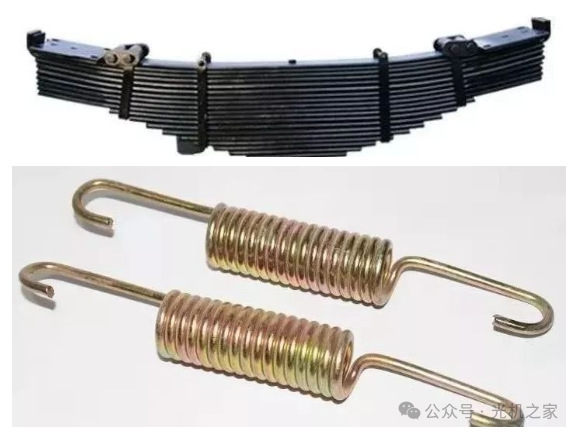
弹簧钢作为机械工程中不可或缺的材料,广泛应用于各类弹簧的制造中,如汽车悬挂弹簧、工业设备弹簧、精密仪表弹簧等。弹簧钢的性能直接决定了弹簧的使用寿命、可靠性及整体机械性能。热处理工艺作为弹簧钢性能提升的重要手段,其优化对弹簧性能的影响深远。本文将探讨弹簧钢中热处理工艺的优化及其对弹簧性能的影响。
一、热处理工艺概述
热处理工艺是通过对钢材进行加热、保温和冷却等步骤,以改变其内部组织结构,从而达到提高材料性能的目的。弹簧钢的热处理工艺通常包括退火、正火、淬火、回火等步骤,以及表面处理如喷丸、氮化等。每种工艺的选择和优化都直接影响弹簧钢的最终性能。
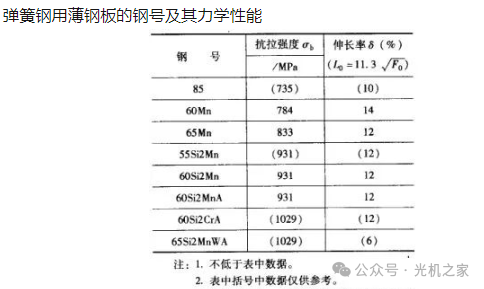
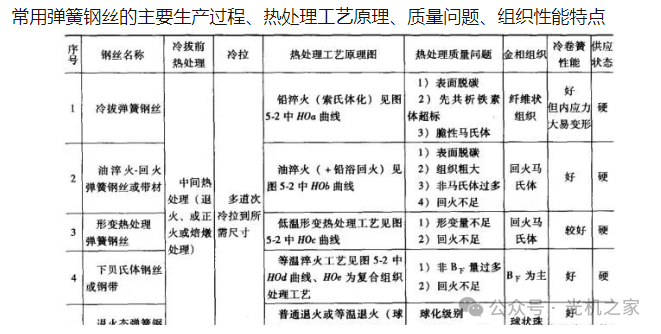
二、弹簧的典型失效方式及危害
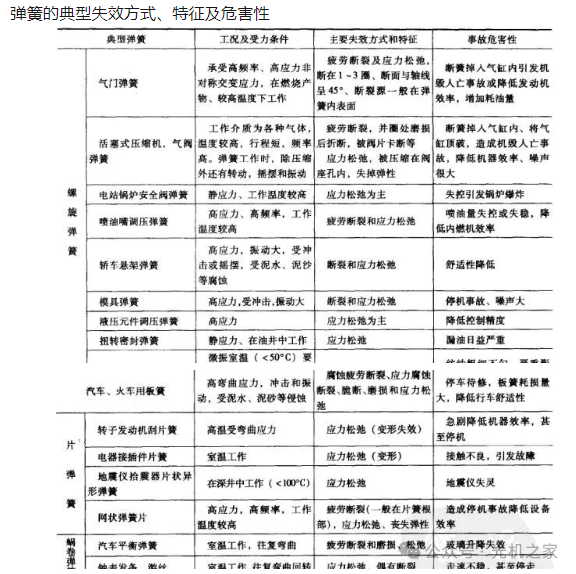
三、热处理工艺优化及其对弹簧性能的影响
1. 淬火工艺优化
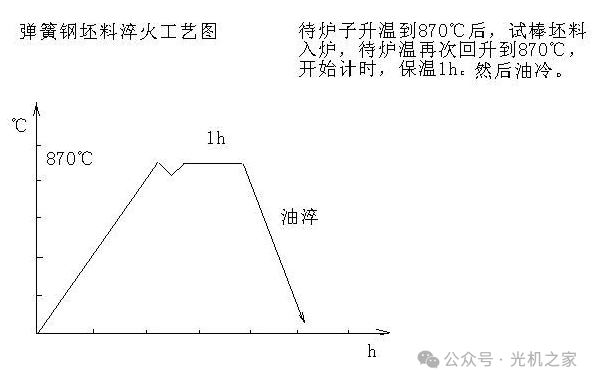
淬火是弹簧钢热处理的第一步,其主要目的是将钢材加热到临界温度以上后迅速冷却,使其组织转变为马氏体,从而获得高硬度和高强度的材料。淬火温度的选择至关重要,既要保证充分奥氏体化,又要保持较细的晶粒。晶粒细化能显著提高弹簧钢的冲击值。
优化措施:淬火温度一般在820~870℃,具体温度需根据钢材成分和所需性能进行调整。同时,淬火介质的选择也影响冷却速率和最终性能,常用的淬火介质有水、油等。优化淬火工艺时,应严格控制加热温度和冷却速率,避免过热和脱碳现象,以保证获得理想的马氏体组织。
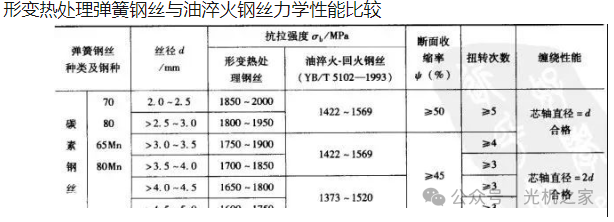
对弹簧性能的影响:淬火后的弹簧钢具有较高的硬度和强度,但韧性相对较差。合理的淬火工艺能显著提升弹簧的承载能力和抗疲劳性能,但过高的淬火温度或过快的冷却速率可能导致脆性增加。
2. 回火工艺优化
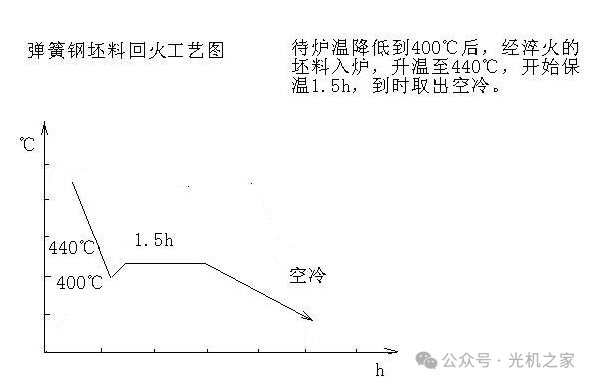
回火是淬火后的必要步骤,其主要目的是消除淬火过程中的内应力和脆性,使弹簧钢获得良好的韧性和韧度。回火温度一般在350~550℃之间,温度越高,弹簧钢的韧性越好,但强度降低的速度也越快。
优化措施:根据弹簧的使用条件和性能要求选择合适的回火温度和时间。对于要求高强度和一定韧性的弹簧,可采用中温回火;对于要求更好韧性的弹簧,可采用高温回火。同时,回火时间要足够长,以确保温度均匀和淬火组织得到充分回复。
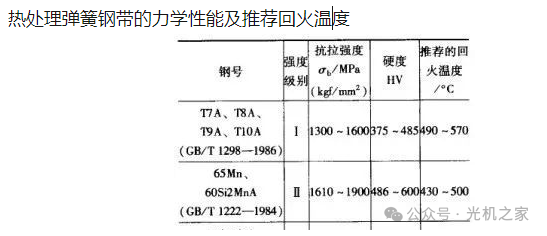
对弹簧性能的影响:回火能显著改善弹簧钢的韧性,减少脆性断裂的风险。合理的回火工艺能使弹簧钢在保持较高强度的同时,获得良好的韧性和疲劳性能。此外,回火还能稳定组织,减少使用过程中因应力集中导致的裂纹和变形。
3. 表面处理工艺优化
表面处理是弹簧钢热处理的最后一步,其主要目的是提高弹簧钢的抗腐蚀性和耐磨性,并使其外观更加美观。表面处理方法包括酸洗、镀锌、镀铬、氮化等。
优化措施:根据弹簧的使用环境和性能要求选择合适的表面处理方法。例如,对于要求高耐磨性的弹簧,可采用氮化处理;对于要求抗腐蚀性的弹簧,可采用镀锌或镀铬处理。同时,应严格控制表面处理过程中的工艺参数,如温度、时间等,以确保处理效果。
对弹簧性能的影响:表面处理能显著提高弹簧钢的抗腐蚀性和耐磨性,延长其使用寿命。氮化处理能在弹簧钢表面形成一层硬度较高的氮化物层,提高其硬度和耐磨性;喷丸处理能去除表面氧化皮和锈蚀物,使表面更加光滑,减少疲劳裂纹和应力集中。
四、热处理工艺优化的重要性
热处理工艺优化对弹簧钢性能的提升具有重要意义。首先,优化热处理工艺能延长弹簧的使用寿命和提高可靠性。通过合理的热处理工艺,使弹簧钢获得最佳的力学性能和表面质量,从而满足各种复杂工况下的使用要求。
其次,热处理工艺优化还能提高生产效率和降低成本。优化后的热处理工艺能降低生产中的不合格品率和修补率,减少材料消耗和工艺流程中的处理时间,从而提高生产效率并降低生产成本。
此外,热处理工艺优化还能推动热处理技术的发展。通过对弹簧钢热处理工艺的深入研究和实践经验积累,可以为其他材料的热处理工艺研究提供有益的经验和参考,推动热处理技术的不断进步。
五、结论
热处理工艺优化对弹簧钢性能的提升具有显著影响。通过合理的淬火、回火和表面处理工艺优化,能使弹簧钢在保持较高强度的同时,获得良好的韧性和疲劳性能。这不仅延长了弹簧的使用寿命和提高了可靠性,还提高了生产效率和降低了成本。因此,在弹簧钢的生产和应用过程中,应重视热处理工艺的优化研究和实践应用。